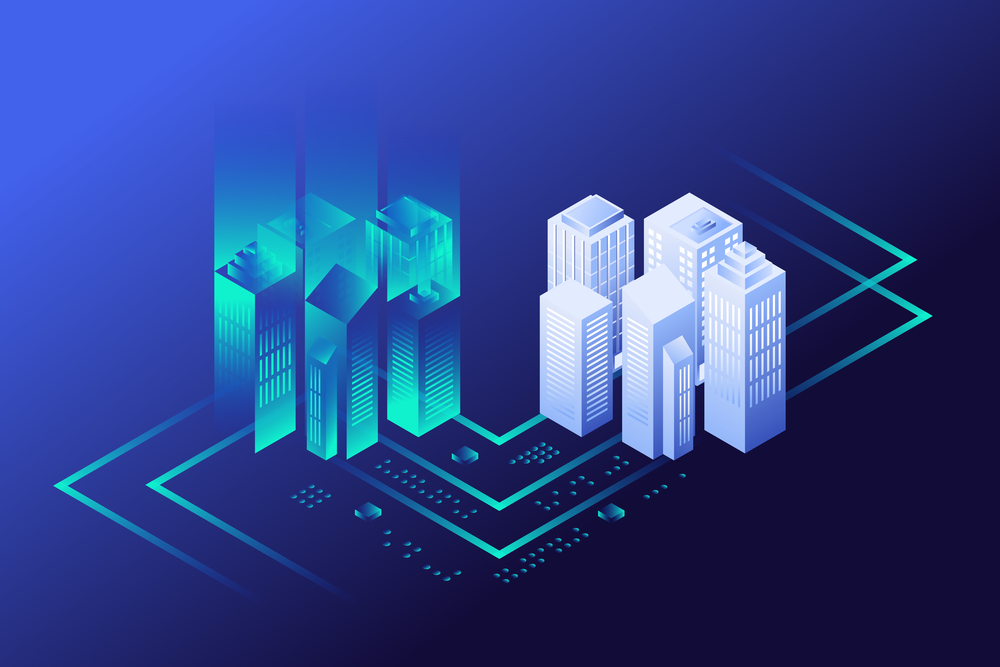
Industry 4.0 – the emerging future of manufacturing – combines software and IoT devices to support faster, smoother, and more cost-effective operations. Getting there, though, depends on tools that provide accurate, real-time insights about floor-level machinery. Also critical: a low-risk way to continually optimize performance and equipment health.
Enter digital twins. They use IoT data to replicate physical machinery (like a robot or conveyor belt) in a virtual environment. And they’re the key to smart manufacturing.
Here, I’ll explain how digital twins work and how manufacturers can use them to improve efficiency and protect the bottom line.
How Real-Time IoT Data Powers Digital Twins
True digital twins are more than static 3D simulations. They rely on real-time data that continuously flows between IoT-monitored equipment and engineers. Here’s what the process looks like:
- IoT sensors collect real-time data about equipment. This could include data about a machine’s position, electrical currents, rotational speed, noise emission, temperature, etc.
- The data feeds into the manufacturer’s cloud storage system. Depending on the sensor hardware, data transmission can occur via WiFi, Bluetooth, cellular, or wide access network (WAN).
- Engineers use cloud data to virtually replicate the monitored equipment. From here, engineers can manipulate this digital twin without actually being on the facility floor. If any changes need to occur to the physical equipment, they can remotely communicate that to nearby workers.
As IoT sensors continue to improve their connectivity with cutting-edge technology (like 5G), they’ll be able to relay larger volumes of data at higher speeds than ever. That means manufacturers can maximize the accuracy and relevancy of every digital twin.
It’s worth noting that although digital twins are often used to simulate equipment or machinery, they can also replicate whole manufacturing environments. For example, if a manufacturer is using connected data loggers to monitor a climate-controlled warehouse, workers can create a digital twin to simulate how sensitive products react to sudden fluctuations in temperature, pressure, or humidity.
In the following sections, we’ll take a look at a few specific ways manufacturers can use digital twins to transform their facility operations.
See also: Surging Growth in the Global Cloud Database and DBaaS Market
Digital Twins Enable Smarter Decision Making
One of the biggest advantages to a digital twin is the ability to remotely track a machine’s operation in real time. And with the right software, AI can recommend adjustments that could extend a machine’s lifetime or improve its performance.
Those two use cases – predictive maintenance and performance optimization – can pave the way for smart manufacturing that protects the bottom line. To illustrate, I’ll walk you through a scenario for each.
Use Case #1: Predictive Maintenance
Imagine an auto manufacturer that’s struggling to keep its automated conveyor belts from breaking down without warning. Engineers can use a series of digital twins to monitor the full conveyor belt system. Thanks to real-time data, they can pinpoint the moment a foreign object gets caught in a machine or a motor starts slowing down – and alert a worker on the floor before the system comes to a halt.
What’s more, AI can use equipment data to, say, notify engineers when a motor has worn down past a certain threshold. It can even suggest an optimal maintenance schedule by comparing real-time and historical data.
The bottom line: with the help of digital twins, manufacturers can slash equipment downtime and keep revenue flowing.
Use Case #2: Performance Optimization
Picture a food and beverage manufacturer that wants to improve the efficiency of its packaging robots. With digital twins, engineers can track each robot’s performance and identify specific components that could be slowing them down.
Then, they can virtually test individual tweaks (like a motor upgrade) and simulate their effectiveness in custom production scenarios. They can even adjust environmental factors, like heat or humidity, to gauge the upgraded robot’s structural resilience. Once the engineers have identified the right changes, they can relay next steps to the right team.
The benefit: digital twins let manufacturers explore ways to create new efficiencies without disrupting equipment on the floor.
Digital Twins Can Be a Product Development Sandbox
So far, we’ve looked at ways digital twins can help manufacturers optimize equipment within their facilities. But they’re also powerful tools for intelligently improving devices in production.
Think of digital twins here as a product development sandbox: engineers can model a near-infinite number of product changes and operational scenarios in a matter of seconds. Most importantly, these changes happen without the need for costly physical rework.
The simulation and testing process is similar to the ones we’ve already explored. The main difference: each model relies on a recent snapshot of IoT data about prototypes versus a true real-time stream. Even so, engineers get a highly accurate prototype simulation that they can virtually manipulate to boost its performance. It’s a low-risk way to test, fail, learn, and create better products.
Don’t Wait to Invest in Digital Twins
Digital twins are a core enabler for Industry 4.0. But the truth is that many firms are already watching this space. The proof: digital twin investments are set to reach $73.5 billion by 2027.
It’s clear that manufacturers using digital twins will gain a leg up in this next phase of industrial innovation. Invest now or risk falling behind.
Jason Hehman is a Client Partner at TXI and the Vertical Lead for Industrial Innovation and Industry 4.0 at TXI. He helps clients come up with innovative solutions to their most difficult challenges by building integrated teams of their own, transforming company cultures, and supporting new products and services that optimize the ways they and their customers do business.